Sonoco Finished Goods Warehouse
Hartsville, South Carolina
Sonoco Products Company, one of the largest producers of diversified consumer packaging, set out to modernize their existing Hartsville facility with the goal of increasing efficiency and improving handling. The project includes a 115,000-square-foot addition of warehouse space, with 23,000 square feet for production.
Their existing plant recycles paper and cardboard waste products into large diameter paper rolls, high-impact retail displays, and packaging. This new addition will be a location for warehousing and shipping the finished goods, while also including the portion of the production line that slices down the large-scale rolls to order for shipping. Building a new finished goods warehouse will help keep finished product clean and protected, improve shipping, and facilitate ordered vehicular circulation around the site. This project is highly important to the company, as it will separate the outbound finished goods from the inbound raw materials being delivered, increasing their warehouse storage, shipped quantities, and overall production. As the lead design team on the project, Carlisle Associates Inc. provided full architectural and engineering design services for Sonoco’s Finished Goods Warehouse (FGW) in Hartsville, South Carolina.
This required multiple trips for documentation and coordination with the Sonoco team to verify the existing conditions and determine the best solutions. There were many challenges to work through. The existing remaining buildings had varying finished floor elevations that would need to be tied together. The new warehouse would be accessible on three sides. It was not possible to maintain a 60’-0” clear yard for more than half the building. Our design team resolved this issue by separating the new FGW with a 4HR fire wall where clearance is 40’-0” or less to protect people, the facility, and their product. The impact was that CAI had to resolve the new heavy foundations sitting on soft soils with a high-water table all while not impacting the existing 100-year-old heavy masonry buildings the FGW would be placed up against. Using helical piers, foam blocks, and other engineered solutions, CAI was able to solve these challenges. Additionally, the FGW incorporated a protected egress alley for the adjacent existing facility’s lower levels. While difficult to design and construct, the project is estimated to save the company about $30 million per year upon completion.
-
Before
Fitting the new finished goods warehouse onto the site required the demolition of existing buildings, a couple of railraod lines, and the associated railroad trestle and canopy.
-
Plan
The red outline shows the perimeter of the new finished goods warehouse and portrays all of the obstacles that the job entailed


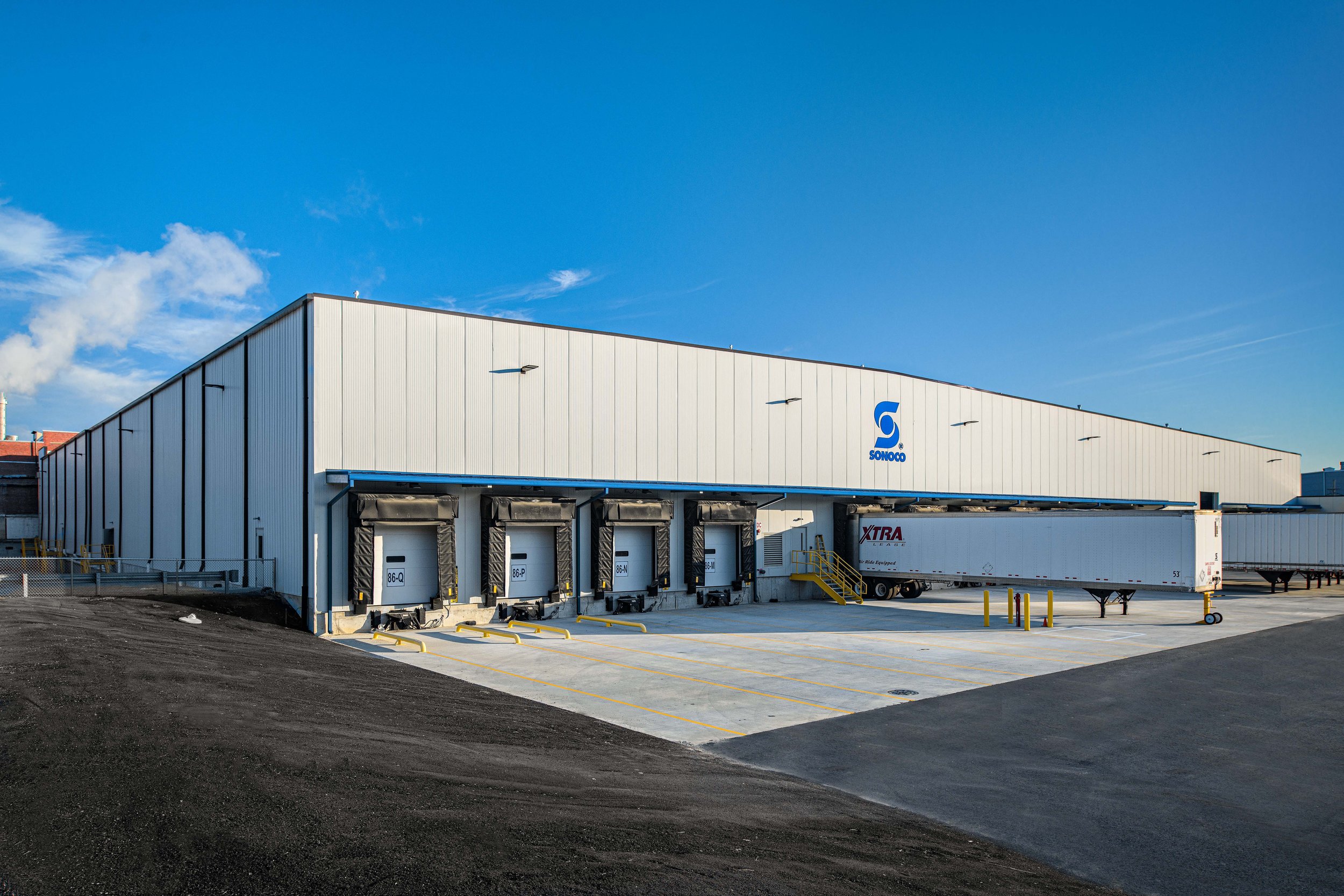
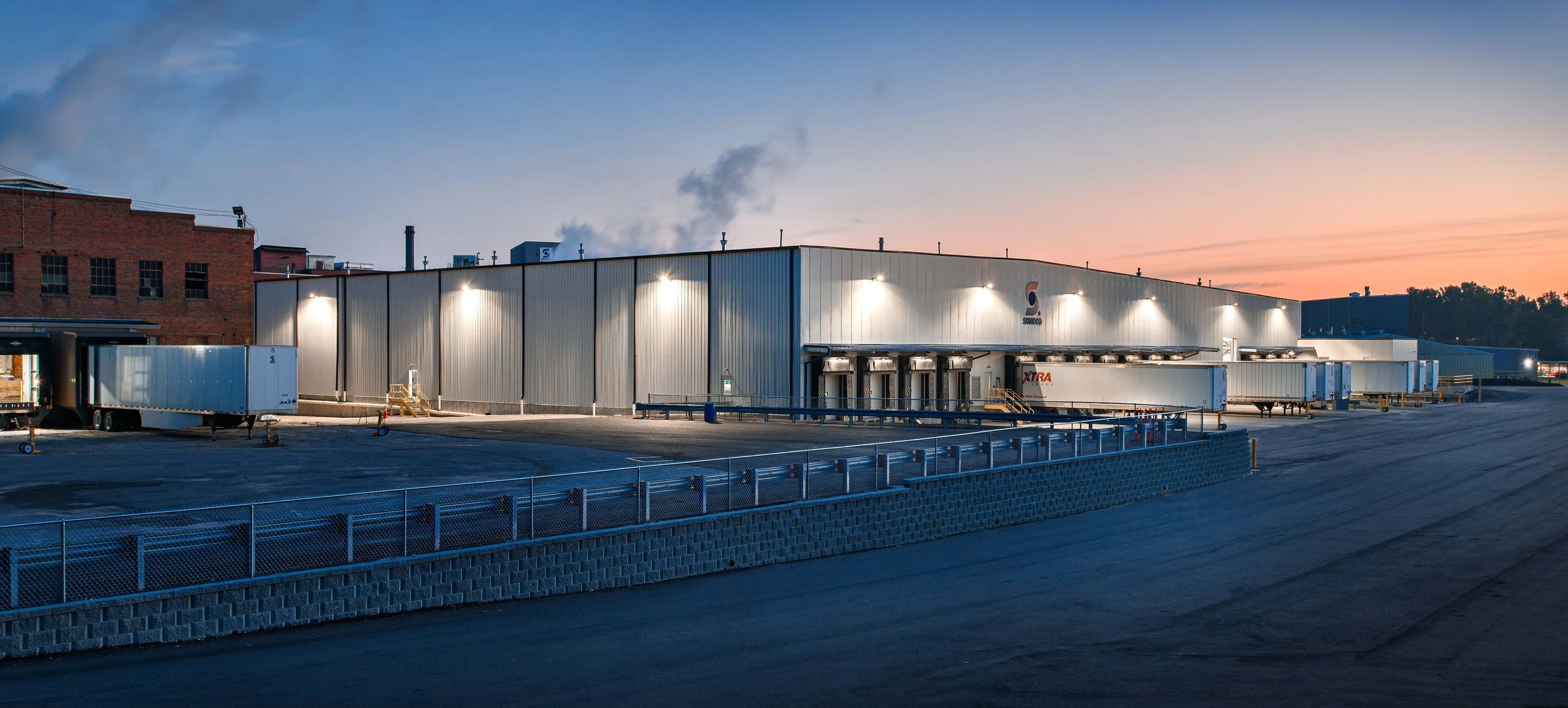
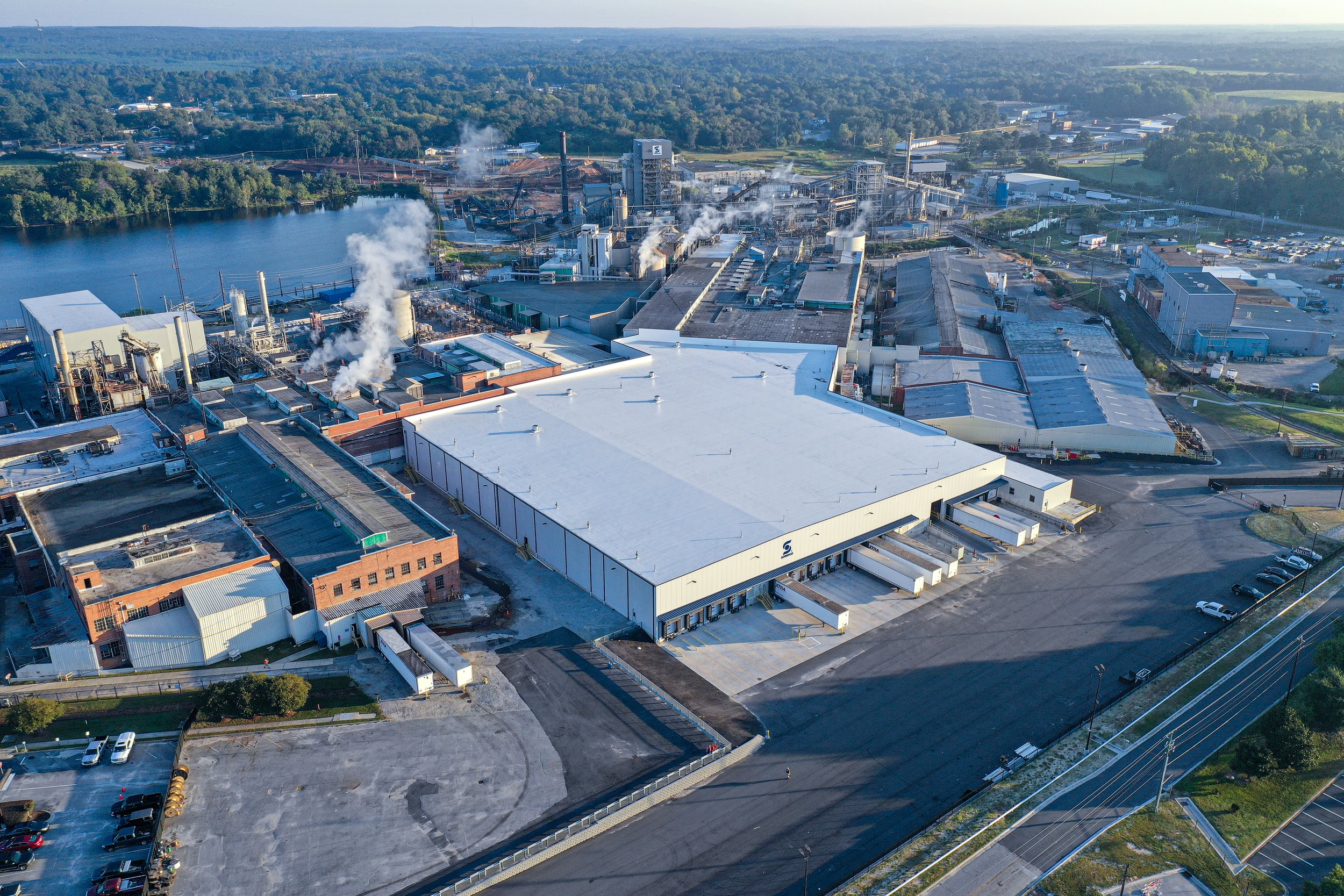